水是重要的啤酒原料,直接影响啤酒的质量和风味特征。特别是麦汁制备用的酿造用水直接参与工艺反应,是麦汁和啤酒的重要组分,被称为啤酒的血液。水中离子对麦汁的组成、发酵的性能和啤酒质量有重要影响,如镁离子有苦涩味,铁离子有铁腥味,锌离子能影响酶活力和酵母新陈代谢,钙离子能调节糖化醪液和麦汁的PH值,保护α--淀粉酶的活力及沉淀蛋白质等。自然界存在的水质量大部分不符合啤酒酿造要求,为了适应工艺需要和提高啤酒质量, 进行处理。主要方式有煮沸法、离子交换法、电渗析法、加石膏改良法及反渗透法等。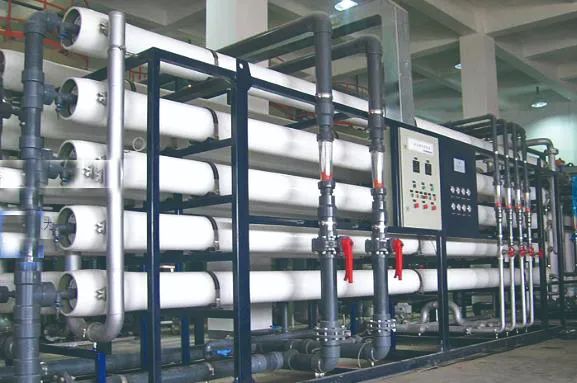
图一:50kl/时反渗透机组
反渗透是渗透的一种反向迁移运动,是在压力驱动下,借助半透膜的选择截留作用,将溶液中的溶质与溶剂分开的分离方法。其原理是在高于溶液渗透压的作用下,依据其他物质不能透过半透膜而将这些物质和水分离开来,见图二。反渗透膜的膜孔径非常小,仅为10A左右,因此能够有效地去除水中的溶解盐类、胶体、微生物、有机物等,去除率高达97-98%。
图二:反渗透机组工作原理示意图
原水 → 多介质过滤器 → 活性碳过滤器 → 精过滤器 高压泵 → 反渗透膜装置 → 纯水罐 → 用水单位多介质过滤器采用无烟煤、石英砂作为过滤介质,去除固体悬浮物、胶体物质及铁锰氧化物;活性炭过滤器采用净水专用果壳活性炭,去除有机物、色度、异味、余氯,使余氯低于0.1mg/L;精过滤器采用5μm的PP熔喷滤芯,去除水中的微粒,使原水水质达到反渗透膜的进水要求;反渗透膜装置采用超低压节能型反渗透膜,有效地去除水中的细菌、胶体、病毒及有机、无机物质。
原水、粗滤净化水、处理水不同时期测的水的质量指标如表一。 表一:原水、净化水及处理水质量指标 单位:德国度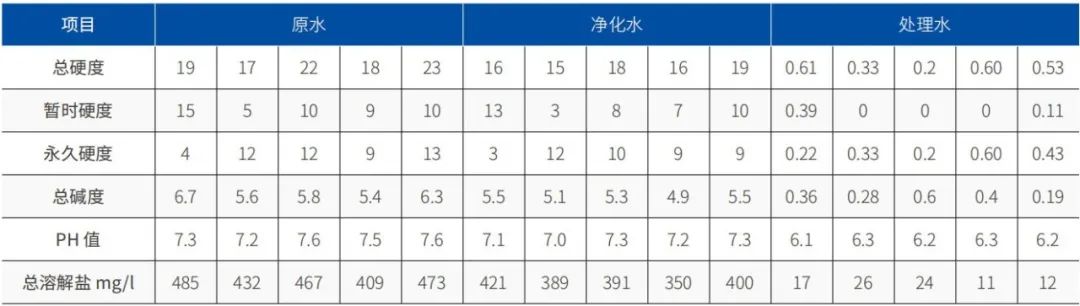
可以看出:原水总硬度在17~23德国度、PH值在7.2~7.6之间。在不同时期暂时硬度和 硬度波动较大,不符合酿造用水要求,不能直接用于啤酒酿造;通过反渗透膜制成的处理水由于PH值太低、总硬度低及水中离子过少等,在啤酒酿造过程中,造成淀粉酶、蛋白酶活性降低、啤酒非生物稳定性差、口味偏淡等,也不能直接用于酿造用水。因此反渗透处理水需与经过粗滤以后的净化水进行混合,混合比例可以根据酿造用水的要求进行确定,再用于酿造生产。混合后的水质量指标见表2。表二:混合水质量指标 单位:德国度
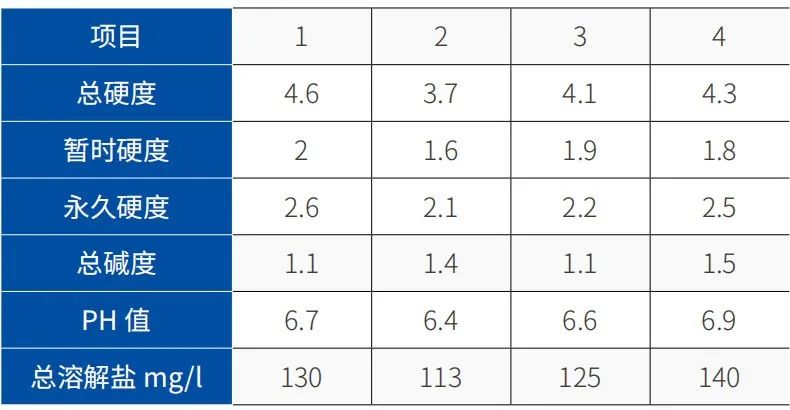
可以看出,处理水和净化水根据需要按比例混合以后,硬度在3~5德国度,碱度在1~1.5德国度,PH值在6.4~7.0,并且酿造用水的质量相对较稳定,减少了因酿造用水质量的波动对啤酒质量的影响,基本能满足酿造用水的要求;在糖化时加少量的酸就能调节糖化醪液的PH值满足要求,提高了啤酒口味质量。同时检测发现,即使处理水和净化水混合以后,酿造用水中的钙离子含量还是比较低,不能满足生产的需要。因此在糖化时还需添加一定量的钙离子,使其含量达到60~90mg/l,以保证蛋白酶、淀粉酶活性及啤酒的非生物稳定性。此外反渗透水可以经过紫外线杀菌去除水中的细菌、病毒、微生物,制成无菌水用于发酵大罐、清酒罐CIP清洗及啤酒稀释用水,也可以用于洗瓶机 一道清水喷淋等。
4.1反渗透系统的预处理工艺设计,已经 可能地去除原水中带来的污染物质,但并不能全部去除,所以反渗透系统污染现象很普遍。幸运的是大多数污染物质通过定期的化学清洗可以被去除。只要预处理工作正常,不存在难以控制的原因,如原水水质改变或无法避免的微生物污染发生,清洗频率可以尽量低。有时候操作失误会导致膜的污染,如回收率太高或加药系统不正常等。膜被污染产水量会下降,脱盐率会下降,进口与浓水之间的压力差会升高。膜清洗可以使一些酸碱药剂(pH2-12条件下),膜清洗药液温度 45℃。许多污染,特别是粘泥类,随时间积累量增加并被压缩且增厚,这样清洗起来就会非常困难。因此清洗周期不要间隔太长。4.2化学清洗标准:如果症状符合下列特点,就应该立即清洗膜元件。
· 压差ΔP上升15%(与初始24 - 48小时的压差值对比)。4.3清洗药箱和其它设备
化学清洗药箱通常是PE或FRP 材质,可以耐受pH范围1-12。清洗温度尽量高些,比如35-40℃。化学清洗不要在15℃ 以下进行,因为清洗效率很低。有时为防止过热,也需要冷却,因此加热和冷却装置对于控制清洗药液温度都是需要的。清洗药箱的体积要足够大,需要考虑压力容器和系统的管路容积,如果计算管路体积比较困难,可以按压力容器的20% 体积计算。清洗时合适的泵,相应阀门、流量计、压力表都需要安装好。
图三:反渗透膜
4.4 清洗程序
1)向清洗水箱中注入RO产品水,清洗液量要满足压力容器和管路体积的需要。向清洗水箱中加入计算好的药剂量,开启清洗泵,闭路循环充分搅拌混合药液。4)将预加热的药液注入管路中,在低压、低流量,将管路中残留的水挤出来并将排出来的水放掉,直到浓水中或循环管路中有药液出现(由清洗液温度或pH值显示)。5)清洗液在RO主机和清洗装置间循环并保持温度,注意观察药液的浊度以判定其有效成分比例。尤其碱洗时如果药液浊度和颜色,发生明显变化,应排放掉原药液重新配制药液。酸洗过程中要检测pH值,在溶解无机盐时要消耗酸液,如果pH值上升0.5个单位,需要加酸。6)循环之后关闭清洗泵浸泡膜元件,有时候浸泡1个小时就足够了,但对于复杂的污染,浸泡10-15个小时很有效果。为保持浸泡期间的温度,可以用小流量循环。7)再循环30-60分钟将膜表面松动的污染物冲走。如果污染比较重,清洗流量高50% 冲洗会有帮助。清洗时压降过大会有问题。建议单支膜压力降小于1.4 bar,多支装压力降小于4.1 bar。清洗流向要与工作时的流向相同。8)排放清洗药液,取样分析药液中污染物的类型和含量,这有利于判定清洗效果和污染的原因。9)用反渗透产水或干净的水,都可以冲洗膜系统。为防止沉淀, 冲洗水温是20℃。10)清洗结束后系统重启,但开始的水 要排放掉直到产水电导和pH值恢复正常。如果系统还需要另一种化学药品清洗,那就要将系统中的水排放掉。注意如果清洗后停机超过24小时,那就用保护液浸泡(1% 亚硫酸氢钠溶液)。如果是多段系统 分段清洗,可以使用同一清洗泵分别清洗,也可以配制多个清洗泵。
4.5杀菌
如反渗透系统发现被微生物粘膜污染,例如微生物黏膜或腐殖物,那么清洗之后应该对系统进行杀菌处理。除了不需要大流量循环外,程序与化学清洗相同。通常使用的杀菌剂有过氧化氢、过乙酸。浓度为400ppm的过乙酸溶液可以用作反渗透系统的杀菌。过乙酸溶液的系统杀菌效果要远好于过氧化氢。操作时要十分小心,不要超过0.2%的浓度。建议间歇性使用,以免连续性使用对膜造成损伤。当使用过乙酸时通常不需要pH值调节。
5.1在反渗透处理水过程中,水中的微粒、胶体粒子或溶质大分子由于与膜存在物理化学相互作用或机械作用,而引起在膜表面或膜孔内吸附、沉积造成膜孔径变小或堵塞, 常见的为碳酸钙垢、硫酸钙垢、金属氧化物垢、硅沉积物及有机或生物沉积物,造成反渗透膜的污染,使处理后的水质量发生波动。因此要定期检测处理水的质量,发现水质量指标发生异常,要对管路进行消毒和反冲洗,使反渗透管路清洁无菌和畅通,保证处理水的质量。5.2可以根据啤酒风格,适当调整处理水和粗滤水混合的比例。需要硬度稍高的酿造用水,可增加净化水的用量。5.3由于反渗透膜对钙离子的透过率几乎为零,处理水的钙离子含量很少,即使在处理水和净化水混合后,水中钙离子的浓度也不能满足酿造用水的要求。因此,要把酿造用水的钙离子作为一项化验指标,定期进行检测。根据结果,在糖化时,补充一部分钙离子,使其浓度达到40~60mg/l,以满足淀粉酶、蛋白酶活性和麦汁煮沸时沉淀蛋白质的需要。5.4在任何情况下不要让带有游离氯的水与复合膜元件接触。如果发生,将会造成膜元件性能下降,而且再也无法恢复其性能。在管路或设备杀菌之后,应确保送往反渗透膜元件的给水中无游离氯时,应通过化验确证。应使用酸溶液来中和残余氯,并确保足够的接触时间以保证反应完全。 5.5在清洗溶液中应避免使用阳离子表面活性剂,因为可能会造成膜元件的不可逆转的污染。5.6 任何反渗透系统的故障会表现为脱盐率下降、产水量降低、压降升高,这三个指标会分别出现或者共同发生。如果三个指标中的一个或多个标准化之后背离了正常值,这就说明需要化学清洗以去除污染和化学结垢。5.7仪表(TDS计、压力表、流量计、pH仪表和温度计)校准是解决任何故障程序的 步。原水和产水的TDS在线仪表可以用便携式仪表校准。需注意安装位置、安装方法、使用方法,应遵守厂家技术规范。5.8浓水密封圈可能在安装时或水力冲击下发生翻转。部分进水会发生短路,没有经过膜元件而从膜与压力容器缝隙中流过,这样实际的回收率就超过了规定值,从而造成膜元件的污染。这种问题的发生是无规律的,早发现多检查是 有效的方法。
图四:仪表的安装
5.9低脱盐率和高产水量是膜被氧化(余氯、溴和臭氧所氧化)的典型症状。其它的氧化剂例如过氧乙酸、过氧化氢等混合物破坏性相对较弱,但是如果存在过量而且与金属催化剂共存时仍然对膜有损坏作用。